
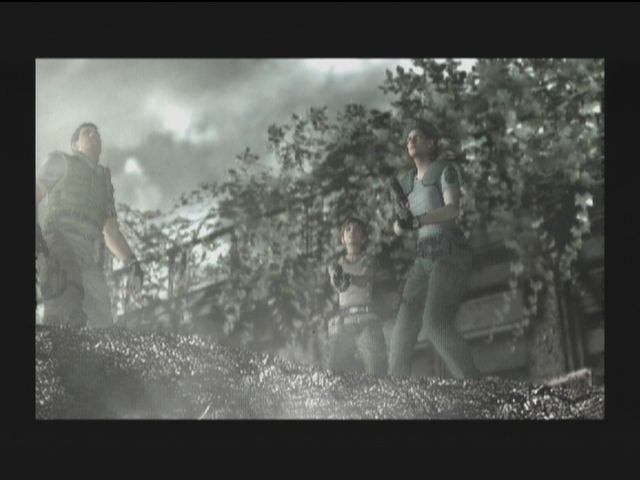
This form of concrete is developed by eliminating fine aggregates from the mixture resulting in concrete which comprises of only large voids and coarse aggregates. This makes it ideal for use in hard to reach spaces and sewer systems. Voids are typically injected through a chemical reaction, or with the use of an air entraining agent.Īerated or foamed concrete does not require flattening, exhibits appropriate thermal insulation, and is self-compacting. This type of lightweight concrete is also known as gas concrete or foamed concrete, since it is developed by introducing large voids into the mortar mass or concrete. However, denser varieties show better bonding results between steel and concrete, along with enhanced protection from steel corrosion. Lightweight aggregate is perfect for pre-cast concrete blocks or steel reinforcements. Weaker aggregates may also be added to the mixture, which has an impact on its thermal conductivity however, doing so may reduce its strength. This form of lightweight concrete is produced using porous and lightweight aggregates including Clay, Shale, Slate, Volcanic Pumice, Ash, or Perlite. Types of Lightweight Concrete Lightweight Aggregate Concrete

LWC is also commonly used to construct interstate and traffic lanes, without adding dead load to existing structures. It guards against steel corrosion by forming a protective layer, which also works to insulate steel structures against rot. For example, utilizing LWC in the Wabash River Bridge allowed builders to reduce project density by 17%, and save 18% in terms of cost – amounting to a whopping $1.7 million.ĭue to LWC’s low thermal conductivity and higher heat resistance, it is now commonly used to insulate water pipes, walls, rooftops, etc. As such, it can be used to successfully build bridges, decks, girders, piers, precast constructions, and high rise buildings with reduced density. LWC is thus ideal for constructing additional flooring on top of older or even newer structures, as it reduces the risk of collapse. This shows how LWC can be used to build formidable structures, especially since the possibility of dead load being transferred from one floor to the next is greatly reduced. One of the most popular structures built with lightweight concrete is the Bank of America Building in Charlotte, N.C. Practical Applications of Lightweight Concrete Hence, LWC remains a cost effective construction material, especially for larger projects.
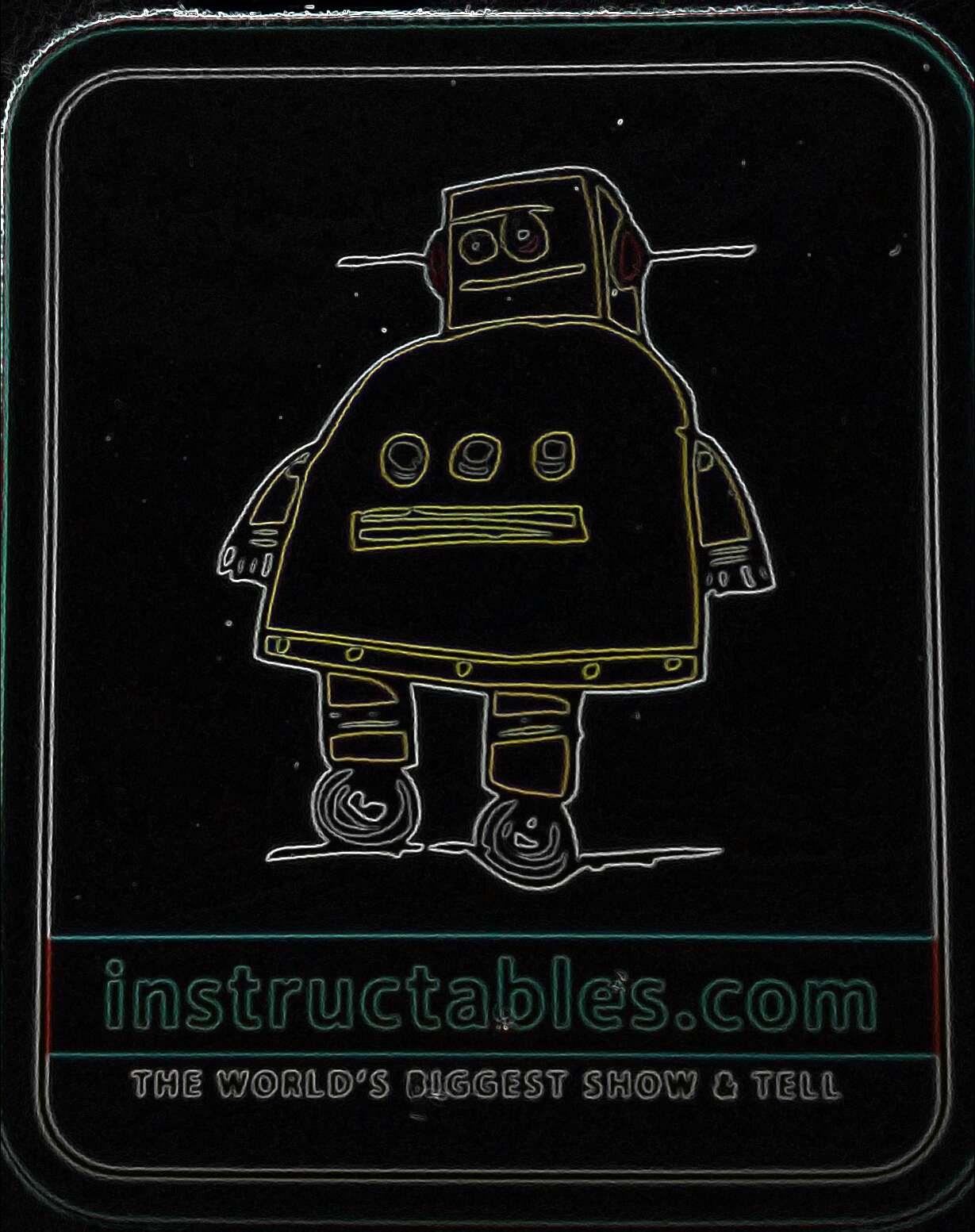
However, projects made with normal concrete require additional material for framing, cladding, and steel reinforcements – ultimately increasing the overall cost. As a result, many believe normal concrete to be cheaper compared to LWC. The use of porous aggregates increases the time it takes to dry hence, to offset this problem, aggregates are pre-soaked in water before being added into the cement.Īs mentioned earlier, normal concrete can weigh between 140 to 150 Lbs/ft³ due to the presence of denser aggregates in their natural state. In contrast to traditional concrete, lightweight concrete has higher water content. Differences between Normal and Lightweight Concrete However, this may compromise the density of the mixture as it requires the addition of more pozzolans and water-reducing admixtures to the concrete. Nevertheless, a higher compressive strength of 7000 to 10,000 psi can be attained with lightweight concrete. It is being increasingly used to build sleek foundations, and has emerged as a viable alternative to regular concrete. This makes lightweight concrete ideal for building modern structures that require minimal cross sections in the foundation. Structural lightweight concrete has an in-place density of 90 to 115 lb/ft³, whereas the density of regular weight concrete ranges from 140 to 150 lb/ft³. Lightweight concrete is a mixture made with lightweight coarse aggregates such as shale, clay, or slate, which give it its characteristic low density.
